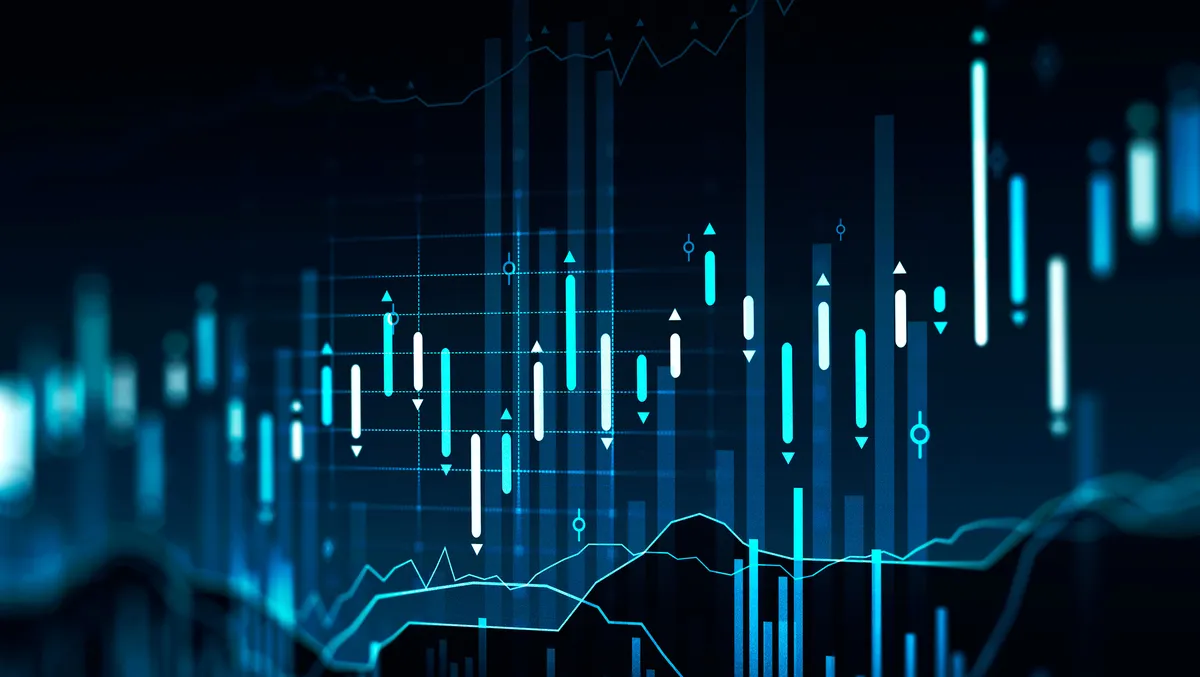
Key considerations for harnessing warehouse data to improve operational excellence
Retailers have more orders, more SKUs, and higher customer expectations. But also, less time for fulfilling orders, less time for order delivery, and less time for taking care of maintenance. That leaves hardly any room for making mistakes.
Consumers are unwilling to forgive incomplete or delayed orders and can easily decide to switch to a competitor. As a result, operational excellence has become the primary goal for retailers (and yet a hidden treasure).
The key to achieving operational excellence is through data. But what are the key data considerations to improving your warehouse operations today?
Consideration 1: Your operation is probably already collecting millions of data points and events
All modern fulfilment facilities (small, medium, or large) require software to handle the operations. Many use a WCS (Warehouse Control System) or WES (Warehouse Execution System). Some use a WMS (Warehouse Management System).
These "higher level" systems are vital to directing facility operations – they answer to the controls layer and the PLC software (which administers manufacturing processes) with sub-second response times. They manage users logging in and logging out, fulfilling orders, assigning SKUs, doing SKU replenishment, and many other tasks.
In addition, your facility is likely running a SCADA (Supervisory Control and Data Acquisition) system, which is highly important for those responsible for maintaining your facility. A SCADA system detects in real time whether an operation is running properly and is often the first point of contact for corrective maintenance.
All these systems (and there might be several more in your operation) collect data. The question is: what can you do with that data?
Consideration 2: You need reliable data to make good decisions
Data from these systems contain precise information about your facility's operations and performance. And precise information allows you to make the best possible choices to maximise the availability, efficiency, and even lifecycle of your operation.
Again, the necessary data is already being generated in your facility, but most retailers are not taking full advantage of it to drive operations. The data can provide answers to important questions such as:
- Are some areas of your site more productive than others?
- Do your operators perform better during certain times of the day?
- Are certain shifts better than others?
- Are certain SKUs causing more problems than others?
- Are certain SKUs always short on inventory?
- Are there any faults in my system which cause more downtime than others?
Speaking about downtime, imagine if your facility has only one hour of downtime per day at a cost of $20,000. (In some cases, it's easily five times more than that.) Any decision that can help you reduce downtime can save you millions of dollars – even more if you operate on multiple sites.
So the data for making good decisions is already there. But you might be lacking the right tool to take full advantage of it.
Consideration 3: You may have the data, but not the analysis you need
Although your WES, WCS, WMS, or even SCADA software may have dashboards and feedback for you, their primary goal is not to aggregate and present the data – that's not what they are designed for. This is why a dedicated analytics tool, like the Dematic Analytics Tool, is crucial.
An analytics tool gathers all operational, maintenance, and equipment data from your systems — and across networks of locations — to provide a single, cohesive view through a suite of dashboards that display uptime, downtime, fault analysis, and much more. By providing real-time access to your data with clear visibility, you can develop and implement action plans to improve your operations by proactively addressing potential issues before they become truly disruptive.
Another important benefit of solutions like the Dematic Analytics Tool is that it can store your very detailed data for multiple years.
This is especially important for operational change, where you need to compare how your systems performed before and after the implementation. A reliable data trend analysis can help future-proof your business.